Product testing at AMS is one of the most important tasks we perform in the process of developing new components for our customers. It is also extremely important when testing stock components. If you’re going to research, engineer, design, and manufacture a performance product it has to function better than the stock part. Gathering data properly is absolutely necessary to gain the most out of a product design.
Q: How do you gather proper data
A:
Isolate The Data:Â First you have to isolate any factors that can affect your test data. Ideally you only want the data you are focusing on changing. You don’t want weather conditions, tuning variations (knock/retard), or state of the car effecting results.
What to watch out for:Â Companies not taking the time to test only what is important. Then, putting out generic data in order to mislead the customer.
Conditions & Test Car/Equipment:Â It should go without saying but you must be using the exact same car and dyno when testing a component. Also, ideally you test in the same weather conditions. Testing a vehicle in 75 deg F summer weather will have vastly different results than in 30 deg F winter temperatures, even when using SAE correction factors, especially on turbocharged engines!
What to watch out for: Companies that base their test on two different cars, dynos, or testing dates. Testing a product in varying weather conditions, not disclosing when it was tested, and with what correction factors are big clues for the consumer to watch out for.
Stabilize A Baseline:Â When we test, we get the car fully up to temperature including engine oil, coolant, and trans/diff fluids. We make a series of pulls with repeatable rest periods in-between to establish a baseline. The first pulls are usually the highest, intercooler and turbo temps are low and stabilize after a few pulls, hence why AMS does not use those pulls in our data sets.
What to watch out for: Companies that cherry pick data to make their product look ideal. Picking the highest gains vs the lowest baseline.
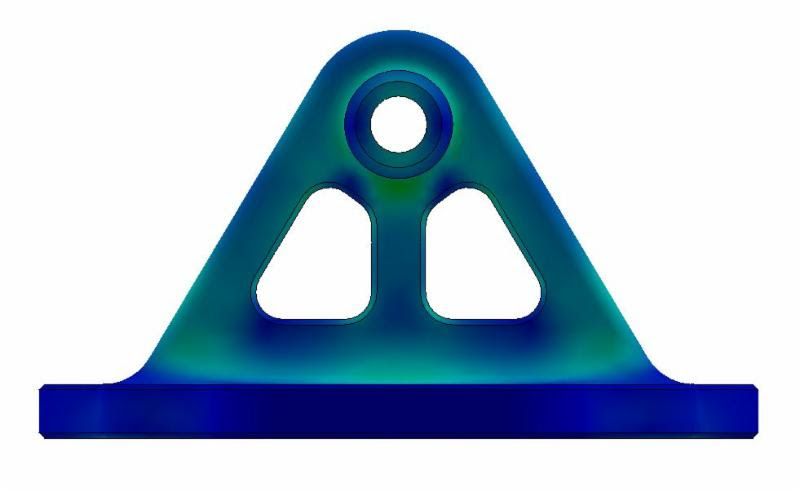
Repeatability:Â The tune also has to be repeatable, meaning you can’t be riding the knock sensor on pump gas and trying to test a part. The timing variation from pull to pull will drastically effect the horsepower and torque, and skew your data.
What to watch out for: Companies that can’t verify or show stable data between runs. A rough looking graph, pushing the limits on pump gas and riding the knock sensor doesn’t allow repeatable results.
Proper Sensors:Â For example, if you’re measuring how efficient a new intercooler is you would gather temperature in and out of the core, along with pressure drop across the core. You would use appropriate sensors that give reliable readings that have minimal resolution errors and are quick responding. Fast response thermocouples and pressure sensors that are appropriately sized for the range of pressure you are gathering, ie don’t use a 100psi range sensor if you’re trying to measure a 0.5psi difference.
What to watch out for: Companies that will use a standard slow response EGT or thermocouple to measure temperatures and have misleading data that lags behind what is really happening. Watch out for pressure data that has more sensor reading variance than the data change being recorded!
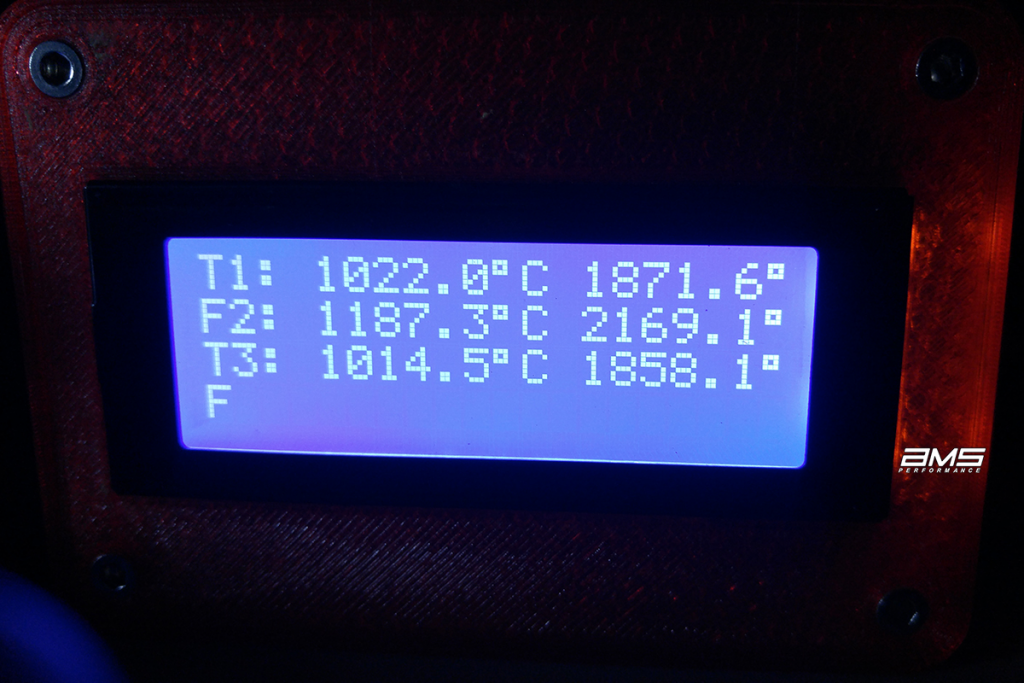
Putting The Data Together:Â Once we have stable measurable data we will take an average of a run/data set before and after a part change for comparison use.
What to watch out for:Â Â A common tactic parts manufacturers use is slapping on a part with no data gathering, making a few pulls and taking the highest reading, which is not only a bad test, it’s misleading to the customers!
Watch as Lance gives you an idea of how this process worked on the INFINITI intake engineering, design, and testing…